Understand and master the design of an aircraft screew propeller (1/2) :
We will see in this tutorial how to build an airplane propeller with HELICIEL. Heliciel allows construction of the geometry and analysis of the propeller's performances . A blade design, with profiles and pitch can be edited. A 3D model is also performed and prototyping will be possible, using the IGS blade file in a cad and prototyping machines. This propeller project will of course be tested without endangering the safety of persons!
Open a model airplane propeller in héliciel
Data to collect (here we took a scale model for example) before starting the construction of our propeller are:
- Estimated flight speed. (120 km/h = 34 m/sec)
- Rotation speed of the motor (8000 Rotation Per Minute) with the best performance (the engine will run at its best speed, it will be fuel efficient and does not suffer from premature wear ..)
- maximum blade length that our plane will be without disturbing the landing phase (140 mm). The propeller is the largest propeller will have the best performance ... if the speed of the blade tip is below the transonic speed (0.7 times the speed of sound so below about 700 km / h). If the speed is higher, the aerodynamic performance degrades and the propeller loses efficiency.
- Size of the motor cover (75 mm), which determine the radius at the blade root, it is not useful for our blades are shaped to cover (unless you want to cool the engine)
- Resistance to advancement (Drag newtons) estimated at the cruising speed. (30 newtons) The drag wings and fins can be studied with HELICIEL in a project to build wings. The drag geometric shapes can be evaluated with mecaflux. The addition of drag forces at the given velocity will be the thrust your propeller must furnish to the given speed.
- Engine torque at that speed of rotation 1.9 Nm
- A torque curve of the engine, according to the speed, will determine whether the requested torque curve of the propeller depending on its rotational speed is always lower than the engine curve..
Enter the "Project specifications"
Tab 1: Project specifications- Tab 1.1 Fluid: click to change the fluid, and select air 20 degrees, and choose altitude 0 meters (click yes to the proposed choice)::
- Tab 1.2 Goal: propeller
- Tab 1.3 operating point:
- fluid velocity: 34 m/s
- Rotation speed. = Preferential RPM: Enter 8000 rev / min
Tab 2.1 Blades Dimensions:
-
Blade length:
- Radius at the blade tip = 140 mm
- Blade root base: we set the radius at the blade root (area where the blade begins to be profiled effectively) to 26% or 36.4 mm, so that it starts at about the engine cover (75 mm of space / 2 gives the radius foot blade )
- Blade width
- Chord at the root: enter 30mm
- Chord at the blade tip: a tapered blade end with a chord of 8 mm
- Chords distribution: we choose in this example, a linear distribution, so click on "linearized" and do not use the slider to change distributions.
Warning: For each modification chord it is imperative to update the distribution of cords by clicking "Linearize". You can then modify this distribution with the cursor. If you want to store a distribution, note the distribution equation, so you can apply it in a future adjustment .....
- The thickness of the blade will not be set because we have chosen the "law of constant profile" in the tab 2.2, with the NACA1408 profile, loaded with the default propeller project . This means that the blade widths (chords) also determines the thickness of the blade (thickness according to chords).
Now we just have to rebuild our blade and test its performance by click onThe result pane shows the performance of our propeller and the 3D prototype tab is updated.) : This function builds the twist of our propeller blade optimized for the operating point described by the speed and the fluid velocity.
- power Kw=( Torque(N.m) X speed(rpm) )/9550
We see that our propeller generates a thrust of 22 newtons, with a torque of 1.1 newton and a shaft power of 947 watts.The calculated thrust ( 22 newtons ) is slightly less than the estimated drag (30 newtons) we estimate that our plane will not reach the required speed, As we have some power margin , engine power (1590 watts), is greater than the shaft power (947 watts), we can try to increase the rotational speed (go to 10 000 rpm) to increase thrust:
- We will rebuild our blade and twisting (cliick
) To match the new operating point and update performance::
And we get our new thrust 33 newtons at 10,000 rpm
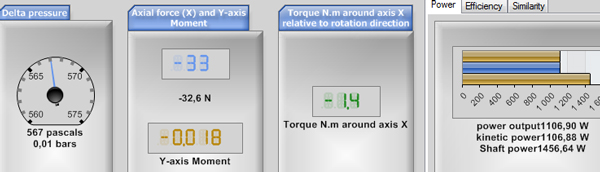
- These 11 newtons of thrust cost us 509 W.
We have chosen the way of the power to increase our thrust, We could have may be in these power save period, try to optimize our propeller! We'll see how to optimize our airplane propeller in the Tutorial propeller aircraft design (2)